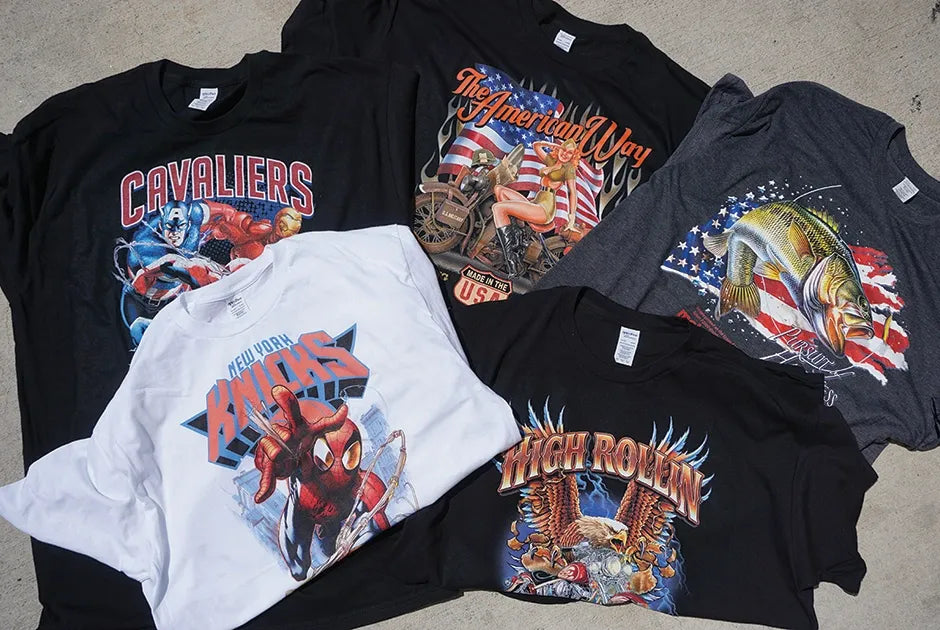
What Does it take to be a Success, in the DTG Printing World
Share
Embarking into the realm of custom apparel printing can be an exciting journey, especially for newcomers. One avenue that stands out for its simplicity and effectiveness is direct-to-garment (DTG) printing. Unlike traditional methods, DTG offers a seamless digital process that's ideal for small-scale projects and intricate designs.
Let's delve into the world of direct-to-garment printers suitable for beginners, helping you navigate your way through this innovative printing technique!
Fundamentally, a direct-to-garment printer functions much like your standard inkjet printer, except it's tailored for fabric printing rather than paper.
To start, you'll treat your garment with a specialized liquid solution. This pre-treatment aids in ink adhesion and enhances color vibrancy on the fabric.
Next, your garment is placed on a platen within the DTG printer. The printer then applies water-based ink directly onto the fabric, layer by layer, bringing your design to life.
Once printed, the ink is cured using a heat press or tunnel dryer, ensuring durability and longevity.
One of DTG's notable advantages over traditional methods is its streamlined setup. It requires minimal preparation time, making it ideal for small batches or unique designs.
Additionally, DTG printing allows for a wide range of colors and intricate details, empowering you to realize even the most complex design visions!
Comparing DTG Printing with Screen Printing When weighing DTG against screen printing, several factors come into play:
Setup efficiency and cost-effectiveness: Screen printing involves creating individual stencils (screens) for each color, which can be time-consuming and costly for small runs. DTG, on the contrary, boasts swift setup times and is economically viable for smaller quantities. Design complexity: DTG excels in rendering detailed, multi-colored designs effortlessly. Screen printing is better suited for simpler designs with fewer colors due to the necessity for separate screens for each color. Texture and durability: Screen-printed designs often have a textured feel and are renowned for their durability. In contrast, DTG prints offer a softer touch as the ink integrates seamlessly into the fabric. Navigating Direct-to-Garment Printing for Beginners While crafting your designs is undeniably exciting, grasping the technical intricacies is key to mastering DTG printing. Here are essential tips to ensure your designs are primed for DTG success:
- Optimal File Formats and Resolution High-resolution images (at least 300 DPI) guarantee sharp, clear designs. Utilize PNG or TIFF formats for DTG printing to maintain transparency and image quality, steering clear of compressed formats like JPEG.
- Precision in Color Management Employ color profiles like Adobe RGB or sRGB for consistent color reproduction. Test prints on sample garments to verify color accuracy across different screens and fabrics.
- Acknowledge DTG's Limitations Printing on dark fabrics with DTG requires a white ink base, which can impact color vibrancy. Adjust designs accordingly for optimal results.
- Embrace RIP Software Invest in RIP software to streamline design-to-print processes, ensuring accurate artwork translation onto fabric, enhanced color management, and detailed print outcomes.
- Prioritize Maintenance Regular maintenance is vital for printer longevity and print quality. Implement daily, weekly, and monthly checklists to uphold printer functionality and performance.
- Learn from Mistakes Experimentation is key. Test prints, refine settings, and adapt to challenges for continual improvement in your DTG printing journey.
- Consider Fabric Compatibility Different fabrics yield varying print results. Opt for high-quality, tightly woven cotton for vibrant prints, while exploring blends for unique textural effects.
By embracing these insights, you'll embark on a rewarding DTG printing experience, crafting bespoke designs with precision and creativity!